Introduction
Diesel generators play a crucial role in providing backup power in various industries, commercial buildings, data centers, hospitals, and residential areas. These generators are relied upon to ensure uninterrupted power supply during periods of grid outages or as a primary power source in off-grid locations. However, like any other mechanical equipment, diesel generators are subject to wear and tear, which can lead to unexpected failures and downtime. To address this issue, predictive maintenance strategies are increasingly being adopted to monitor the health of diesel generators and prevent costly breakdowns. This article explores the importance of predictive maintenance for diesel generators and discusses the key techniques and technologies used in this approach.
Importance of Predictive Maintenance for Diesel Generators
Predictive maintenance is a proactive approach to maintenance that involves monitoring the condition of equipment in real-time to identify potential issues before they escalate into major problems. In the case of diesel generators, predictive maintenance is essential for several reasons:
1. Minimizing Downtime: Downtime due to generator failures can have significant financial implications for businesses. By implementing predictive maintenance strategies, organizations can detect potential issues early and schedule maintenance activities during planned downtime, thus minimizing the impact on operations.
2. Extending Equipment Lifespan: Regular maintenance based on predictive analytics can help extend the lifespan of diesel generators by addressing issues promptly and preventing further damage. This can result in cost savings by reducing the frequency of major repairs or premature replacements.
3. Improving Efficiency: A well-maintained diesel generator operates more efficiently, consuming less fuel and producing lower emissions. Predictive maintenance can help optimize generator performance by addressing issues such as fouled fuel injectors or clogged filters that can impact efficiency.
4. Enhancing Safety: Diesel generators pose safety risks if not properly maintained. Regular monitoring through predictive maintenance can help identify potential safety hazards and prevent accidents related to generator operation.
Key Techniques for Predictive Maintenance of Diesel Generators
Predictive maintenance for diesel generators involves the use of various techniques and technologies to monitor the condition of critical components and predict potential failures. Some of the key techniques commonly employed in predictive maintenance of diesel generators include:
1. Oil Analysis: Monitoring the condition of the engine oil can provide valuable insights into the health of a diesel generator. Oil analysis involves collecting oil samples at regular intervals and analyzing them for contaminants, wear particles, and other indicators of engine condition. By tracking changes in oil quality, maintenance teams can identify issues such as excessive wear, fuel dilution, or coolant leaks that may lead to engine failure.
2. Vibration Analysis: Vibration analysis is a powerful tool for detecting mechanical issues in diesel generators. By monitoring vibration levels at various points on the generator, maintenance teams can identify abnormalities such as misalignment, unbalanced components, or bearing wear. Anomalies in vibration patterns can indicate potential failures, allowing maintenance personnel to take corrective action before a breakdown occurs.
3. Thermography: Thermal imaging cameras can be used to detect hot spots and overheating in critical components of a diesel generator. By conducting regular thermographic inspections, maintenance teams can identify issues such as faulty electrical connections, overheated bearings, or inadequate cooling that may lead to component failure. Early detection of thermal anomalies can prevent costly repairs and downtime.
4. Remote Monitoring: Remote monitoring systems allow real-time monitoring of diesel generator parameters such as fuel levels, coolant temperature, oil pressure, and battery voltage. By connecting generators to a centralized monitoring platform, maintenance teams can receive alerts for abnormal conditions and track performance trends over time. Remote monitoring enables predictive maintenance by providing actionable insights into the health status of diesel generators.
5. Condition-Based Monitoring: Condition-based monitoring involves tracking key performance indicators (KPIs) of diesel generators to assess their operational health. KPIs such as fuel consumption, runtime hours, output voltage, and load levels can provide valuable data for predicting potential failures. By establishing baseline values for these parameters and setting thresholds for alerts, maintenance teams can proactively address issues before they impact generator performance.
Technologies for Predictive Maintenance of Diesel Generators
In addition to the techniques mentioned above, several technologies are used to support predictive maintenance of diesel generators. These technologies leverage data analytics, artificial intelligence, and machine learning to improve the accuracy and efficiency of maintenance practices. Some of the key technologies used in predictive maintenance of diesel generators include:
1. useful reference : Predictive analytics involves analyzing historical data and performance trends to forecast future events, such as equipment failures. By collecting and analyzing data from sensors, monitoring systems, and maintenance records, organizations can identify patterns and anomalies that indicate potential issues with diesel generators. Predictive analytics enables maintenance teams to make data-driven decisions and prioritize maintenance activities based on risk assessments.
2. Internet of Things (IoT): IoT technology enables the connectivity of devices and sensors to a central platform for real-time monitoring and control. In the context of diesel generators, IoT devices can collect data on engine parameters, fuel consumption, temperature, and other relevant metrics. By leveraging IoT technology, organizations can remotely monitor generator performance, receive alerts for abnormal conditions, and track maintenance activities from anywhere, improving operational efficiency and reliability.
3. Machine Learning: Machine learning algorithms can analyze large volumes of data to identify patterns and anomalies that may indicate potential failures in diesel generators. By training machine learning models on historical data, organizations can develop predictive maintenance models that can forecast equipment failures with high accuracy. Machine learning can also optimize maintenance schedules and predict the remaining useful life of critical components, enabling proactive maintenance strategies.
4. Digital Twin: A digital twin is a virtual replica of a physical asset, such as a diesel generator, that simulates its behavior and performance in real-time. By creating a digital twin of a diesel generator, organizations can monitor its operation, simulate different scenarios, and predict maintenance needs without disrupting actual operations. Digital twins enable predictive maintenance by providing a virtual representation of the generator that can be used to test maintenance strategies and optimize performance.
Implementation Challenges and Best Practices
While predictive maintenance offers numerous benefits for diesel generators, implementing a successful predictive maintenance program comes with its own set of challenges. Some of the common challenges organizations may face include:
1. Data Quality and Integration: Effective predictive maintenance relies on accurate and timely data from various sources, including sensors, monitoring systems, and historical records. Ensuring data quality and integrating data from disparate sources can be challenging, especially in complex environments with legacy systems and siloed data.
2. Resource Constraints: Implementing predictive maintenance requires investment in technology, training, and resources to collect, analyze, and act on data. Organizations may face resource constraints in terms of budget, expertise, and workforce to deploy and maintain predictive maintenance systems effectively.
3. Change Management: Shifting from a reactive maintenance approach to a proactive predictive maintenance strategy requires a cultural shift within an organization. Resistance to change, lack of buy-in from stakeholders, and organizational silos can hinder the successful implementation of predictive maintenance initiatives.
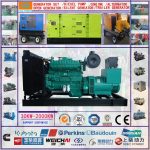
To overcome these challenges and maximize the benefits of predictive maintenance for diesel generators, organizations can follow best practices such as:
1. Establish Clear Objectives: Define clear maintenance objectives and key performance indicators for predictive maintenance initiatives to align them with business goals and priorities.
2. Invest in Training and Skills Development: Provide training and upskilling opportunities for maintenance personnel to enhance their knowledge of predictive maintenance techniques and technologies.
3. Collaborate Across Departments: Foster collaboration between maintenance, operations, and IT departments to ensure seamless integration of predictive maintenance systems and processes.
4. Start Small and Scale Up: Begin with pilot projects or proof-of-concept initiatives to test predictive maintenance technologies and demonstrate their value before scaling up across the organization.
Conclusion
Predictive maintenance plays a critical role in enhancing the reliability, efficiency, and safety of diesel generators in various applications. By leveraging advanced techniques and technologies such as oil analysis, vibration analysis, thermography, remote monitoring, predictive analytics, IoT, machine learning, and digital twins, organizations can proactively monitor the health of diesel generators and predict potential failures before they occur. While implementing predictive maintenance programs may pose challenges, following best practices and focusing on clear objectives can help organizations maximize the benefits of predictive maintenance and optimize the performance of their diesel generators. By prioritizing predictive maintenance as a strategic investment, organizations can ensure uninterrupted power supply, extend equipment lifespan, and reduce maintenance costs in the long run.